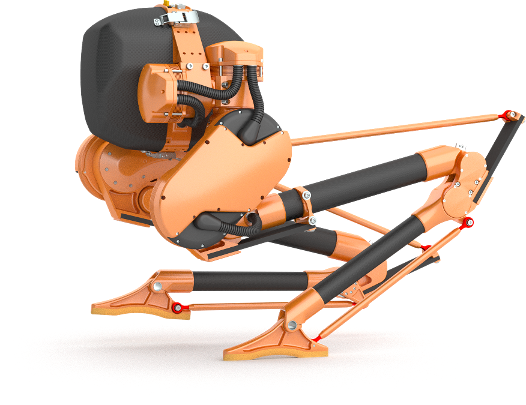
Impact Absorbsion via Mechanical Design
Advisor: Johnathan Hurst - Agility Robotics
Cassie is a bipedal robot that walks with quiet actuators. However, her hard feet create loud impacts, putting stress on the mechanical parts, as well as hindering human robot interaction. Using a combination of silicones and foams, I created new foot designs in order to reduce the peak walking impact without hindering current locomotion controls. We tested the designs on force plate and with a simulated walking gait to measure peak forces and time to peak force. We then tested the top designs on the Cassie robot both in standing phase and walking phase to insure the controls were not heavily affected. The top design (a hexagon honeycomb) decreased the peak force during impact by over 47% and increased the time to peak force by over 600%. Consequently, the impact of each step was reduced by over 90%. The design also integrated seamlessly into Cassie’s current controls.
Design Constraints
At the time, the robotic locomotion controls did not contain velocity matching, meaning each foot slammed into the ground with the full force of the motors for each step. Additionally, the robot relied on the stiffness of the feet to provide accurate balance control. Therefore, to be used in locomotion, the new feet needed to be complient enough to absorb the impact of walking, while stiff enough not to interfere with the balance algorithm.
Design Methedology
Various foot designs were explored within two design spaces: geometry and material. Within geometry, honycombs, procedural diamonds were explored. Within materials, a combination of foams, silicones, and the patented gel from Purple Matress was explored.
Geometries
For all of these designs, foam was added within the geometries
- The collapsable cone (left) was created to systematically absorb the impact as the cone collapses. It was proven to be incompatible with the robots control algorithm.
- The diamonds gemoetry (middle) was the unique geometry of Purple Mattress. This patented technology designed to absorb fast impulses and reduce impacts. This absorbed much of the impact, and was compatible with the robots control algorithm.
- The hexagon geometry (right) incorporated a honycomb pattern on the bottom of the foot. We explored both horizontal loading as shown as well as vertical loading, where the honeycombs faced outward and the side of the honeycomb absorbed the impact. Horizontal loading created the best absorption of the honeycomb designs. This geometry outperformed all other geometries, and was compatible with the robots control algorithm.
While the honeycomb design worked best for decreasing the peak force on impact, after the honeycomb collapsed, only the complience of the materials was able to absorb the impact. To increase the time before collapse (thus decreasing the impact overall), so foam was added in between the honeycomb design to provide more absorption.
Materials
To provide both structure and complience, a variety of silicone’s were explored. While durometer is labeled for each material, it is a qualitative instead of a quantitative measure. Therefore, each materials was tested on a Force Sensor to analyze the compliance. Ecoflex 30 was chosen due to its high strain per a given force). Using the same evaluation criteria, FoamItIV was also chosen. All the materials were from SmoothOn, a silicone and foam manufacturing company.